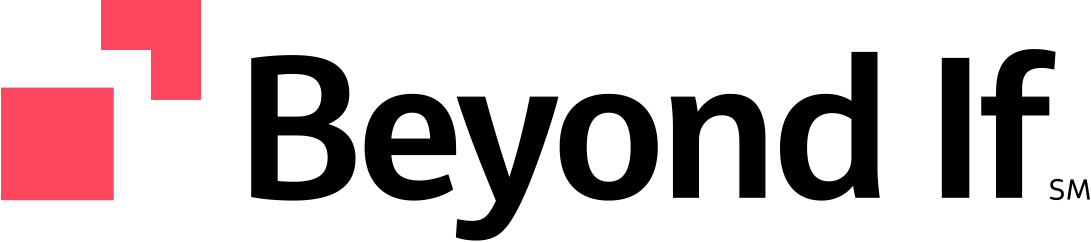
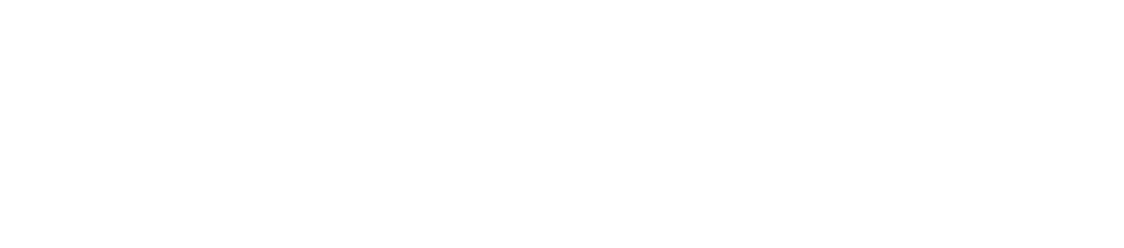
Sit down with our visionary team of thinkers, dreamers and doers to see what a day in the life is like.
A curated selection of some of the top-listened to and trending podcast episodes from our popular If/When podcast series, which has over 7M downloads to date.
Together with our visionary partner, PA Consulting, we're establishing our position in high end advisory services, creating a springboard to expand in high value offerings beyond the core.
At Jacobs, we're challenging today to reinvent tomorrow by solving the world's most critical problems for thriving cities, resilient environments, mission-critical outcomes, operational advancement, scientific discovery and cutting-edge manufacturing, turning abstract ideas into realities that transform the world for good. With approximately $16 billion in annual revenue and a talent force of more than 60,000, Jacobs provides a full spectrum of professional services including consulting, technical, scientific and project delivery for the government and private sector.
Jacobs. A world where you can.
As climate change threatens water security around the world, more communities are turning to water reuse as a resilient water supply solution and embracing the OneWater principle that all water has value. Jacobs has been supporting clients with water reuse programs for decades, beginning with the first applications of advanced wastewater treatment technologies in the 1960s. We provide our clients with a full range of services, from water reuse feasibility studies to design, construction and operations.
As our clients navigate the digital transformation and growing cyber risks, we have positioned ourselves at the forefront of this growth, adding digital capabilities, products and tools to serve a growing set of customers.
The only certainty about the future is uncertainty. Resilience is an attribute of a smarter planet, and requires planning and adapting ahead of potential threats. We help our clients survive, recover, adapt and thrive.
As a purpose-led company, we know we have a pivotal role to play in addressing the climate emergency. We consider this not only good business, but our duty to channel our technology-enabled expertise and capabilities toward benefitting people and the planet.
For more than 30 years, Jacobs has been responsible for planning and implementing Lead and Copper Rule-related strategies which protect millions of people in the U.S. and Canada. Our work includes enhanced water quality monitoring strategies, sampling plan development, harvested pipe-scale analysis, lead service line inventories and replacement plans, corrosion control studies and the incorporation of equity and environmental justice considerations into compliance programs.
Jacobs is working to help clients across the United States secure federal funding for projects that make our cities and communities more connected and sustainable. Working hand-in-hand with clients from coast to coast and everywhere in between, Jacobs develops bold, innovative solutions to address the nation’s toughest challenges.
Now more than ever, we appreciate the hard work, sacrifice and dedication of the medical profession in ensuring the health and safety of our communities.
Together, we are stronger. Together, we can transform the future.
We work in partnership, delivering some of the most challenging, diverse and innovative projects and programs globally across multiple sectors. We integrate complex interfaces across planning, procurement and delivery to help unlock better social, environmental and economic outcomes from mega and giga projects.
We’ve provided design-build services to the water sector for over 25 years and delivered more than 150 projects. We offer fully integrated design-build and design-build-operate capabilities to tackle the most complex water challenges and work in close collaboration with our clients.
Stories that capture our partnerships and innovative impact for a more connected, sustainable world
The average temperature on Earth is 57 degrees Fahrenheit. On Venus, temperatures consistently reach a blazing 840 degrees, and as the planet closest to the sun – Mercury’s hottest temperatures hit up to 869 degrees. As space exploration advances, we need to be prepared for things to heat up.
That’s why our team works with Kennedy Space Center to manufacture heat-resistant tiles for use on space vehicles as part of our Test and Operations Support Contract (TOSC) at the Kennedy Space Center.
As NASA’s primary launch center for human spaceflight since 1968, ensuring the safety and reliability of various spacecraft and personnel at Kennedy Space Center – including temperature protection not only for vehicles, but also spacesuits and portable life support systems – is mission critical.
However, the excess heat-resistant tile scraps manufactured at Kennedy aren’t easy to get rid of, because even though they’re not hazardous, they are controlled by International Traffic in Arms Regulations (ITAR). Projected to be produced at a rate of 4,000 pounds per year, the coated ceramic material waste was rapidly becoming a problem to store and dispose of.
But what if we showed you how Jacobs’ innovative solution transformed a problematic waste into a valuable resource in just a few easy steps, contributing to recycling, reuse and waste diversion goals and creating a lasting benefit for Kennedy Space Center?
pounds of heat-resistant tile waste diverted and reused
in savings by eliminating disposal costs (approximate)
“This creative solution illustrates the ‘out-of-the-box’ thinking that inspires all KSC employees to look for innovative fixes for difficult problems.”
Jim LaRocque
Jacobs Director of Safety and Mission Assurance
The heat-resistant tile scraps at Kennedy Space Center previously had just one possible identified destination for disposal – a secure landfill in Atlanta. However, our team didn’t have a contractual agreement with the landfill and thus, shipping and securing material sent there would be highly costly.
In lieu of high costs and additional landfill waste, engineering, technical and environmental personnel at the Thermal Protection System Facility (TPSF) began seeking other avenues for the waste. The team determined that the material could be demilitarized, which would remove the ITAR export control concern, by reducing the size of the billet material to chunks resembling gravel and a powder form.
A commercial crusher yielded pieces around ½ inch and afterward material was reground to make smaller and Portland cement was added to create a mixture that can be used in various jobs where crushed concrete can be utilized.
Now, this mixed material is being staged at Kennedy’s Demolition and Construction Reuse Yard (DARCY) for use by onsite contractors after being mixed with water to make solidified concrete. Jacobs has even used this material for filler at a newly acquired area at the Kennedy Space Center railyard, where our construction management facilities are relocating from another location.
This innovative solution transformed a problematic waste into a valuable resource in a few easy steps, and in the end the material recycled into concrete is benefitting contractors and Kennedy Space Center alike. Recycled concrete materials from DARCY have been applied on numerous projects, including paving and construction around Kennedy Space Center and even repairs to a wave-damaged seawall and Hurricane-eroded shoreline.
To date, we’ve diverted more than 7,000 pounds of tile material and concrete for reutilization – positively contributing to our team’s and Kennedy’s environmental goals and fully meeting the responsibilities associated with ITAR and Export Control requirements.
When it comes to meeting NASA launch dates, plenty goes on behind-the-scenes to make liftoff possible. What if we showed you how Jacobs’ predictive, data-driven maintenance approach keeps Kennedy Space Center’s systems running smoothly?
Jacobs Engineering Group Inc., and NASA, recently achieved a major milestone at Kennedy Space Center (KSC) as the modified mobile launcher (ML), sitting atop a refurbished Crawler Transporter (CT-2), took its maiden voyage to Launch Pad 39B and then to the Vehicle Assembly Building for fit checks and testing. The ML will support NASA's new Space Launch System (SLS) rocket and the Orion spacecraft during processing and launch.
The Jacobs team supported NASA rolling out the Artemis I rocket from the Vehicle Assembly Building (VAB) to Launch Pad 39B at NASA's Kennedy Space Center (KSC) in preparation of final prelaunch tests of the Space Launch System (SLS). Artemis I, a flight test of the most powerful rocket NASA has ever built, will be the first mission in NASA's new deep space human exploration program, which aims to land the first woman and the first person of color on the moon and establish sustainable exploration in preparation for missions to Mars.
Jacobs began a new era of advanced, affordable space radar payloads with its Mango One satellite achieving a successful on-orbit performance. On Jan. 24, 2021, Jacobs' Mango One satellite was launched from Cape Canaveral, Florida, aboard the SpaceX Falcon 9 Transporter One rideshare mission to a sun synchronous orbit.