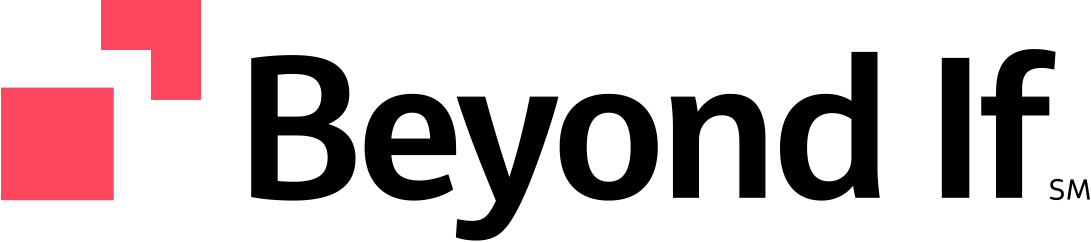
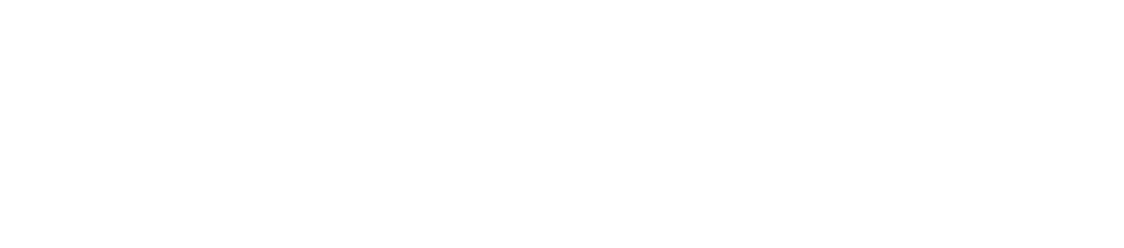
As a purpose-led company, we know we have a pivotal role to play in addressing the climate emergency. We consider this not only good business, but our duty to channel our technology-enabled expertise and capabilities toward benefitting people and the planet.
We work in partnership, delivering some of the most challenging, diverse and innovative projects and programs globally across multiple sectors. We integrate complex interfaces across planning, procurement and delivery to help unlock better social, environmental and economic outcomes from mega and giga projects.
For more than 30 years, Jacobs has been responsible for planning and implementing Lead and Copper Rule-related strategies which protect millions of people in the U.S. and Canada. Our work includes enhanced water quality monitoring strategies, sampling plan development, harvested pipe-scale analysis, lead service line inventories and replacement plans, corrosion control studies and the incorporation of equity and environmental justice considerations into compliance programs.
As our clients navigate the digital transformation and growing cyber risks, we have positioned ourselves at the forefront of this growth, adding digital capabilities, products and tools to serve a growing set of customers.
Sit down with our visionary team of thinkers, dreamers and doers to see what a day in the life is like.
A curated selection of some of the top-listened to and trending podcast episodes from our popular If/When podcast series, which has over 7M downloads to date.
Together with our visionary partner, PA Consulting, we're establishing our position in high end advisory services, creating a springboard to expand in high value offerings beyond the core.
At Jacobs, we're challenging today to reinvent tomorrow by solving the world's most critical problems for thriving cities, resilient environments, mission-critical outcomes, operational advancement, scientific discovery and cutting-edge manufacturing, turning abstract ideas into realities that transform the world for good. With approximately $16 billion in annual revenue and a talent force of more than 60,000, Jacobs provides a full spectrum of professional services including consulting, technical, scientific and project delivery for the government and private sector.
Jacobs. A world where you can.
As climate change threatens water security around the world, more communities are turning to water reuse as a resilient water supply solution and embracing the OneWater principle that all water has value. Jacobs has been supporting clients with water reuse programs for decades, beginning with the first applications of advanced wastewater treatment technologies in the 1960s. We provide our clients with a full range of services, from water reuse feasibility studies to design, construction and operations.
The only certainty about the future is uncertainty. Resilience is an attribute of a smarter planet, and requires planning and adapting ahead of potential threats. We help our clients survive, recover, adapt and thrive.
Jacobs is working to help clients across the United States secure federal funding for projects that make our cities and communities more connected and sustainable. Working hand-in-hand with clients from coast to coast and everywhere in between, Jacobs develops bold, innovative solutions to address the nation’s toughest challenges.
Now more than ever, we appreciate the hard work, sacrifice and dedication of the medical profession in ensuring the health and safety of our communities.
Together, we are stronger. Together, we can transform the future.
We’ve provided design-build services to the water sector for over 25 years and delivered more than 150 projects. We offer fully integrated design-build and design-build-operate capabilities to tackle the most complex water challenges and work in close collaboration with our clients.
Stories that capture our partnerships and innovative impact for a more connected, sustainable world
What’s the common thread between Minnesota’s professional baseball team, Vin Diesel and Lindsay Lohan in The Parent Trap? They’re all twins.
About one in every 32 children is born a twin, accounting for roughly three percent of the population and ironically, both Jacobs Global Digital Solutions Director Raja Kadiyala and one of the Replica™ developers Matt Deavenport, fathered twins. The twinning rate has doubled over the last two decades but spotting a set of twins at the supermarket or on your TV screen is still a fun, somewhat remarkable occurrence. In today’s technological world however, digital representations of physical assets, processes and systems – or digital twins – are rapidly becoming a preferred practice across markets from buildings and railway lines to wastewater treatment and manufacturing plants.
By 2020, IDC expects that 30% of Forbes Global 2000 companies will use data from digital twins of Internet of Things (IoT) -connected products and assets to improve product innovation success rates and organization productivity.
But what if we showed you how a Jacobs-designed simulation platform and digital analytics are rapidly developing digital twin models – right now – for water and industrial water-related processes, helping a customer improve operation performance, while minimizing energy and chemical usage?
reduction in energy consumption using control logic operational improvements [confidential private sector client]
when Gartner predicted digital twins would reach peak productivity
“We surveyed 30 of our water and wastewater utility partners about big data management in 2017. Resoundingly, respondents noted that the Internet of Things and big data analytics could not only optimize their operations, but also predict system failures before catastrophic results. Digital replicas of actual systems, processes and assets can be used for synthetic data generation, prediction, optimization and scenario analysis, helping utilities unleash the power of data to drive unprecedented savings.”
Raja Kadiyala
Jacobs Global Digital Solutions Director
New digital technologies are delivering more sophisticated and interconnected infrastructure solutions than ever before. At the same time, these technologies are increasing both the volume and the quality of data at our fingertips. IoT-connected devices generate around 2.5 quintillion bytes worth of data each day, which can be used to drive better project, asset management and business outcomes.
With sensor prices declining by an expected 50% in the last decade, implementing new technology like digital twins is more affordable than ever before. Digital twins are underpinned by a rich pool of data, made up of information from various sources or “modules”’ brought together in a single digital space or Common Data Environment (CDE). The modules vary depending on individual project and client requirements and can be adjusted over the project lifecycle to reflect the data requirements at each stage of construction.
When one of our clients faced poor performance from their industrial water distribution system that fed key production processes, they turned to Jacobs to drive savings and limit process interruptions and downtime through digital twin analytics.
We developed the Replica digital twin software platform to quickly produce simulations of the client’s water and industrial water processes. Using these hi-fidelity dynamic simulation models, Replica Hydraulics™ and Replica Controls™ accurately portrayed intricate process dynamics and allowed what-if scenarios to be carried out in the digital domain. Replica also allows teams to validate the optimized solutions within the physical process control system (SCADA) hardware to bridge the divide between the digital simulation and the physical hardware.
This pivotal tool allowed our client to improve their operation performance, while lessening the amount of energy they used. Through the development of a digital twin, we could understand system dynamics at a much deeper level, leading to the identification of process improvements. We then validated improvements under a wide set of operating conditions and can perform further validation by linking the digital twin with the revised control logic on the physical process control system. This bridge between the simulated environment with the digital twin to the physical environment allows us to vet the end solution prior to final implementation – and for this client, these identified process improvements helped reduce energy consumption by 33%.