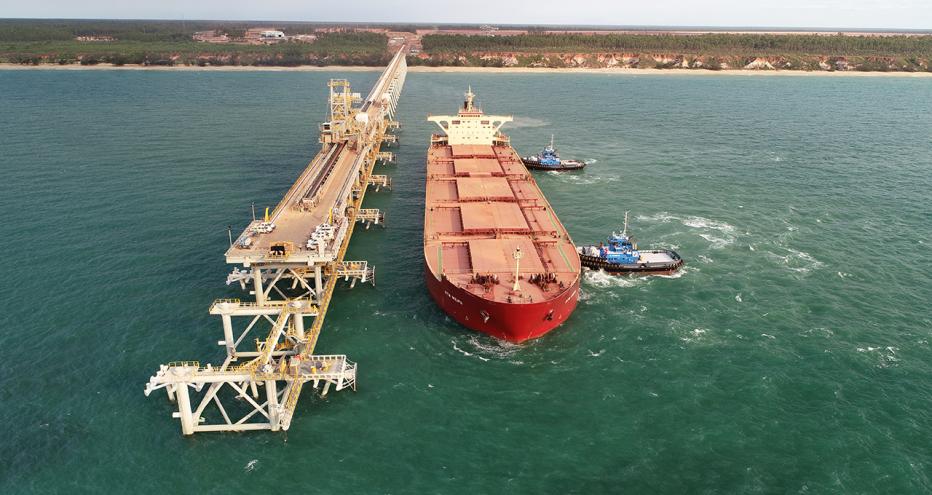
The first shipment of Amrun bauxite on ‘RTM Weipa’ sets sail from Chith Export Facility six weeks ahead of schedule in December 2018. Image courtesy of Rio Tinto.
Rio Tinto’s Amrun bauxite mine in far North Queensland has the capacity to export over 22 million tonnes of bauxite each year for processing into aluminum from its Chith Export Facility near Weipa.
When Jacobs engineers were asked to provide design engineering services for the marine works for the Chith Export Facility, risk, cost and schedule challenges meant looking outside traditional ‘stick-build’ construction methods. The team partnered with Rio Tinto, McConnell Dowell and Bechtel to deliver an innovative large-scale modular design and construction method for the wharf structure that significantly improved project outcomes.
Today, the export facility includes a 650-meter long jetty and 350-meter long wharf with a single-sided berth capable of loading Mini Cape-sized vessels. The wharf has the potential to be expanded to a two-sided berth, capable of loading larger Cape size ships in the future.
Schedule, cost and risk challenges prompt new thinking
The project’s remote location presented numerous challenges, including logistical challenges transporting construction plant, equipment and materials to the site, in addition to safety risks with over water work and work-at-heights.
Overcoming these challenges demanded different thinking and, in true partnership spirit, the combined team (Rio Tinto, Jacobs, McConnell Dowell and Bechtel) broke down organizational barriers to work closely every step of the way.
Instead of independent dolphin and wharf support structures utilizing a large number of driven steel piles, Jacobs engineers proposed using a series of jacketed wharf with integrated dolphin (JWD) modules and deck modules that could be constructed off site, delivered and lifted into position by heavy lift ship. The team had already successfully used modular approaches on previous projects and knew the approach could deliver significant advantages to this project.
Manufactured as a three-dimensional braced tubular steel structure, each JWD module would weigh in at almost 750 tonne and support a 54-meter-long deck module, weighing up to 1200 tonne. Each JWD module would incorporate a fully fitted-out dolphin on one side and the primary framing to support a future dolphin on the opposite side, allowing for future expansion of the export terminal. The 350-meter long Chith wharf structure required seven JWD modules and six wharf deck modules to construct.
Construction logistics were front of mind throughout the design process and the team worked closely with construction contractor, McConnell Dowell, to integrate constructability into the design. The modules were designed to the maximum size and weight possible for transport and installation using cranes onboard the heavy lift ship, which involved close collaboration with the freight provider, Big Lift.
Engineers undertook an Order of Magnitude Study on the innovative design approach and the concept was proved to not only be valid, but to also offer numerous benefits to the project, including significant cost and schedule savings, construction quality and reduced safety risks.
The wharf was constructed on site over approximately 12-months by McConnell Dowell, with construction oversight by the project’s Engineering, Procurement and Construction Management (EPCM), Bechtel. Our engineers continued to provide technical support throughout the fabrication and construction process.
Modular approach delivers significant outcomes
Using the innovative modular design approach reduced on site construction time by 12-months and removed 300,000 hours of high-risk work over water and at height activities on site. The construction of the wharf supported the project’s critical path activities being reduced by three months, delivering significant cost and scheduling savings. The wharf design also reduced the number of permanent piles required for installation from 100 to 28, minimizing the environmental impact to the surrounding area and marine life. .
“Starting with the end in mind was key to the project success,” said Jacobs Ports & Maritime Executive Market Director Dr. Colin Skipper. “A collaborative design approach, designing for constructability and taking a holistic view of material, fabrication and construction costs were key to delivering improved project outcomes for Rio Tinto.”
The diversity in thinking and breadth of experience from the combined team saw Rio Tinto’s state-of-the-art facility delivered safely, efficiently and with minimal environmental impact – a win-win for all.
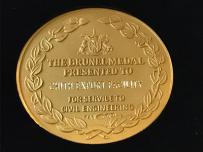
Recognition and Awards
This project is paving the way for future global wharf construction projects by advancing the future of the industry in a safe, cost effective and replicable manner. The project has been recognized with a number of awards:
- 2019 – Recipient of the Brunel Medal for Excellence in Civil Engineering at the Institute of Civil Engineers Awards 2019
- 2019 – Recipient of the Australian Construction Achievement Award presented by Australian Contractors Association and Engineers Australia
- 2018 – National Winner in Category 6: Projects over $75m at the National Civil Contractors Federation Earth Awards 2018
- 2018 – State Winner in Category 6: Projects over $75m at the Queensland Civil Contractors Federation Earth Awards 2018
- 2018 – Shortlisted in the Design Innovation Category at the Consult Australia 2019 Awards for Excellence