Amrun Chith Export Facility
The innovative method used to construct the Chith Export Facility improved safety, costs, had scheduling benefits and minimized environmental impact
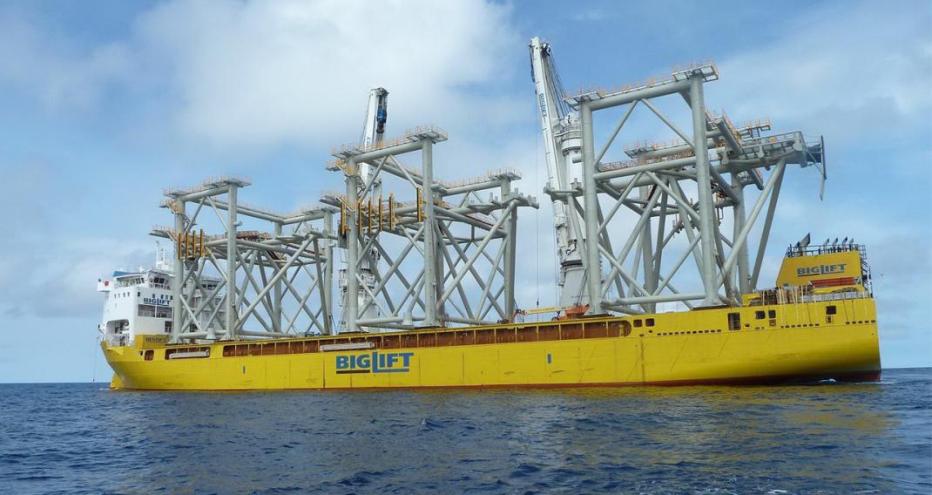
Rio Tinto’s Amrun Project located south of the Embley River, between Weipa and Aurukun in Far North Queensland, revolutionised the design and construction of wharf infrastructure through a collaborative approach between Rio Tinto, its EPCM Bechtel, Jacobs, and McConnell Dowell Constructors.
-
$ 30 M
direct savings attributed to the JWD innovation
-
300 K
labor hours taken off site from high risk work over water and work-at-height construction activities
-
28
permanent wharf and dolphin piles installed (reduced from 100)
“Jacobs brings unequaled talent and innovation to deliver more to our clients on their projects. Our leading-edge solution is a first-of-a-kind design that achieves safety, function, quality, cost, schedule, constructability and sustainability.”
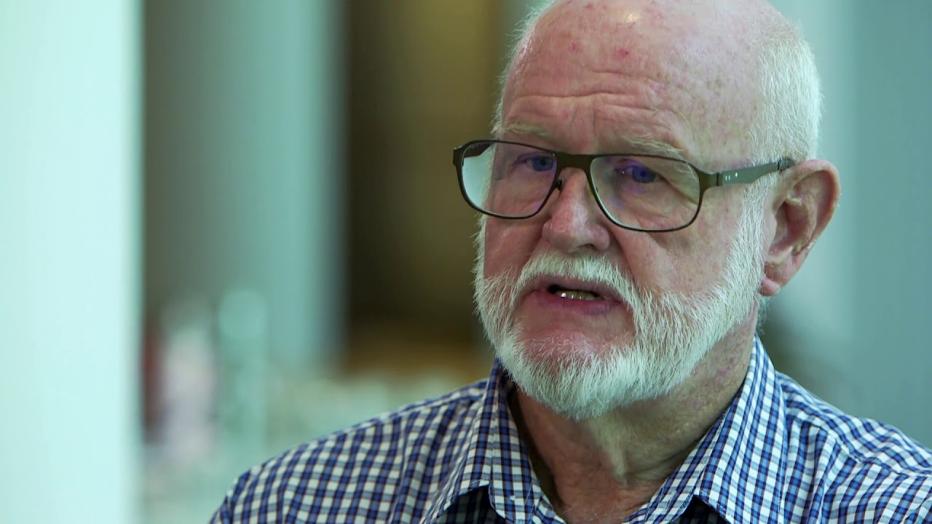
Chith Export Facility: A New Approach
To address logistical challenges in a remote location and deliver amongst an ambitious project schedule, Jacobs investigated an innovative modular design solution for the wharf’s deck and substructure, which also minimized safety and environmental risks.
Over two-months, Jacobs completed and presented an Order of Magnitude Study on the integration of separate dolphin and wharf support structures in the form of a jacketed wharf with integral dolphins (JWD) innovation. This rigorous study developed definition on the design, fabrication, heavy lift shipping and the site installation methods. The concept was proved to be valid and offer numerous benefits to the project, including significant cost and schedule savings, and a reduction in risks.
Jacobs completed the engineering design and documentation and provided technical support and construction oversight for the fabrication and site installation works. The jackets and modules were successfully installed on site over a three-month period.
The project reformed the design of wharf infrastructure by moving away from a traditional stick-built design concept to a modularized construction approach. Supporting a 12-month reduction in overall on-site construction activities, achieving three months off the project critical path schedule, and saving over 300,000 site labor hours, this innovation has resulted in safer project execution by vastly reducing high-risk work activities performed over water and at height. The wharf design also reduced the number of permanent piles required for installation from 100 to 28, minimizing the environmental impact to the surrounding area and marine life. Designed by Jacobs and constructed by McConnell Dowell, with constructability input and construction oversight by Bechtel, Rio Tinto’s state-of-the-art facility has been delivered safely, efficiently and with minimal environmental impact.
-
Amrun Chith export facility under construction © Rio Tinto
-
Amrun Chith export facility under construction © Rio Tinto
-
Amrun Chith export facility first ship departure © Rio Tinto
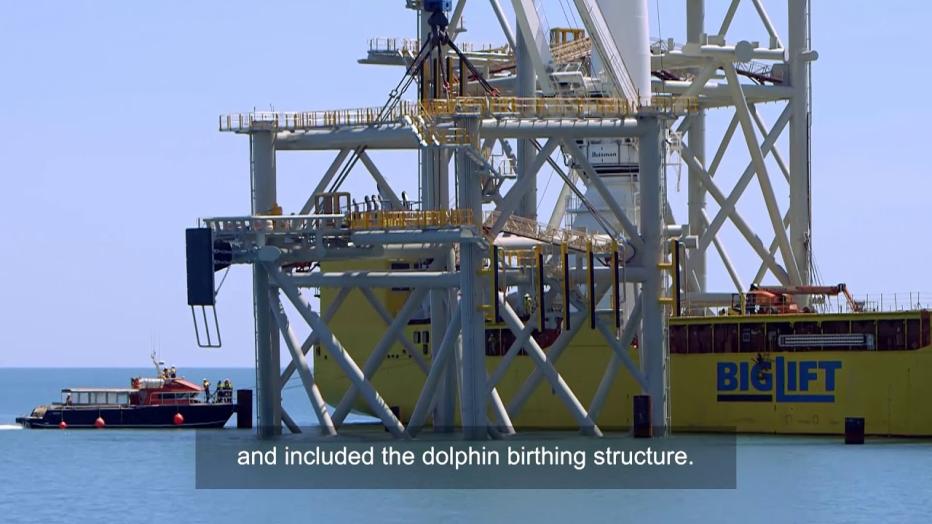